- #EC
- #オムニソーター
2023.05.23
「人とロボットが共存する」一歩ずつ自動化を推進してきたEC物流企業の取り組みとは
株式会社スミレ・ジョイント・ロジ
はじめに
1991年(平成3年)の設立以来、「進化する物流サービス+売れる環境+笑顔」を企業理念に掲げ、埼玉県を拠点に通販物流代行サービスを提供している株式会社スミレ・ジョイント・ロジ様。
スミレ・ジョイント・ロジ様では、フルフィルメントサービスを行う中で、効率的に業務を進めるためロボットによる自動化を推進しており、2022年12月に立体型仕分けロボットOmniSorter(オムニソーター)を導入いただきました。
今回は、同社 代表取締役CEOの山口様と、物流部 草加第一センター 主任 の杉田様に、導入に至った経緯や導入したことによる現場での変化などについて、お話をうかがいました。
導入の経緯
---- 御社では倉庫内の自動化として既に複数の機械を導入しています。いつ頃から取り組みを始められていたのですか?
山口様:約7年前から少しずつ機械を導入してきました。最初のきっかけは、人による作業のムラをなくそうと思い、「機械だったらそれが安定するのではないか」と考えた所がスタートでした。
それから数年経って、今度は労働人口が減っていくというニュースが流れ始めました。テクノロジーの進化も相まって、当時は「世の中にある業種の半分ぐらいはAIとかDXで無くなります」みたいな話で騒がれていましたね。
---- 機械の導入を決めたときの従業員の方の反応はいかがでしたか?
山口様:従業員の反応はさまざまでした。「機械を入れたら自分の仕事が無くなってしまうのではないか」など、ネガティブな意見も多数ありました。
そのような従業員の意見に対し、私は「今いるあなたたちを辞めさせるようなことは絶対にない」と伝えました。「機械は人がスイッチを入れないと動かないし、エラーが出たら人が直さないといけない。そのために今いる従業員みんなが必要です」と。
いまは若い従業員たちが一生懸命箱詰めや荷物を運んだりしているけれども、高齢になった時に同じ作業をするのは肉体的にも大変です。であれば、機械のボタンを押してエラーを修正する作業の方がはるかに楽ですよね。
「だから早い段階で機械に馴染んで、操作方法など率先して覚えてほしい」と、これが説得する上で重要なキーワードでした。
---- 人間と機械の共存ということですね。
山口様:「機械を導入する=省人化」というイメージがありますが、私にはそういう気持ちはありません。人間と機械は必ず共存するものだと思っています。常にそのような気持ちで自動化の導入を進めています。
自動化に対する思いとポイント
---- 自動化といっても工程ごとや、完全自動化などあると思います。自動化に求められるポイントってなんでしょうか?
山口様:我々の扱っている倉庫は古い倉庫も多く、大手企業の最新の物流倉庫とは全く違います。でも、物流業界の90パーセント以上が中小零細企業で大半が我々のような倉庫です。
やっぱりみんなが憧れるのは大手企業のような大きい完全自動化されたような倉庫です。ですが、床や消防の問題、ランニングコストなど、実際には多くの問題があります。なので、自分たちで取り組める部分から進めていく必要があると考えています。
まず大事なのは現場に耳を傾けて、どこを簡略化して自動化したら一番作業しやすくなるのかをヒアリングして、足りないところを少しずつ補っていくことです。「強制的にこの機械を入れます」ではなく、「箱を作るのが大変です」と言われたら製函機を入れよう、「梱包するのに人が足りません」と言われたら梱包機を入れようといった形で。
従業員が困っているところに対して自動化を進めていくことが、結果として結びついてくると思いますね。従業員も自動化に対して前向きに考えてくれています。
---- 少しずつ進めていくことが大事なんですね。
山口様:そうですね。そしてやはり一番大事なことは、いかに人が使いやすいかということです。これは機械を入れてみて本当によくわかりました。
機械もそれぞれ特色がありますが、まだまだ人の手のサポートが必要な部分があるんです。例えば、梱包機だとフィルムが無くなったら交換が必要ですよね。この交換するという作業も「誰か」であってはダメなんです。「誰でも」できなきゃいけない。なので、弊社ではパート従業員でも交換ができるように教育しています。
---- 人の教育も徹底されているのですね。
山口様:周りの物流会社の方とお話するときも、自動化についての話題はよく上がります。私は「絶対に早く入れたほうがいいですよ」ってアドバイスをしています。併せて一番時間がかかるのは人の教育だということも伝えています。
機械の扱い方は、最初に誰か1人が覚えることは簡単です。でもそれを「誰でも」できるようにならないと効率は上がっていかない。社内の文化を築き上げながら機械と共存していくというのは時間がかかることなんです。
---- 人が使いやすいという部分について、どのような軸で判断をされているのですか?
山口様:私のような経営側は機械の自動化というと効率を求めてしまうものですが、現場は徹底的にユーザビリティです。
例えば、商品を置く台の高さだったり、読み取りやすいセンサーの角度だったり。あと、エラーが出ないとか。経営側と現場で心配することが全然違うのです。なので、両方ともうまく当てはまるような形で進める必要があります。
---- たしかに投資対効果とユーザビリティって、目線が全く違いますね。
山口様:機械のわかりやすいところとして、マックス値がわかるところです。この仕様とこの設定であれば、これぐらいの作業量を処理できると。人ができることは、そのマックス値にするためにどう動くか、どう環境を整えるかということです。人間のコミュニケーションや情報共有、操作教育などで、いかに理想に近づけるかを考えなくてはなりません。
OmniSorterを導入して得られた効果
---- 今回OmniSorterを導入したことによる、現場側の業務の変化について教えてください。
杉田様:OmniSorterの導入以前にも、他社の仕分け装置を使用していました。他社の仕分け装置は48間口で、処理スピードは1時間で100オーダーいかないぐらいでした。
OmniSorterは60間口で、1時間で150~200オーダーを仕分けられるので、全然違います。仕分け作業が断然早くなったので、導入してよかったと思います。
---- 仕分け作業が早くなったとのことですが、その分の空いた時間はどのように活用しているのですか?
杉田様:倉庫内を整理整頓する時間を創出することができました。仕分け作業に大量の折りたたみコンテナを使用するのですが、重なっている状態だと幅も高さもあり、通路にあると邪魔になることもありました。それを畳んで片付けをする時間を作れたので、倉庫内が綺麗に整理されている状態が保たれています。
---- 実際にOmniSorterで商品を流すにあたり、得意な商品と苦手な商品について教えてください。
杉田様:得意な商品は、形がしっかりしているものです。正方形や長方形など、四角いものは基本的に流しやすいです。逆に苦手な商品は、丸みを帯びているものです。コンベアに流した時に商品が動いてバーコードが読めないことがあります。
他には、ガラスや陶器などの衝撃で割れる恐れがある商品です。また、クッションなど大きい商品も、カゴがすぐに満杯になってしまったりするので、手仕分けを行っています。
---- 小さい商品はトレイに乗せて流したりもしていますね。
杉田様:取り扱っている商品には小物や薄いシールが多く、そのまま流すことが難しい場合があります。その場合はマニュアルスキャンをした後に、トレイの上に乗せて流しています。
また、クリアファイルや紙などの薄い商品に関しては、更にファイルを挟んで厚みを足してから流すなど工夫をしています。
仕分け工程を自動化したことで見えた次の課題
---- 仕分け工程が早くなったことで、今度はその上流工程のピッキングが課題と伺っています。
杉田様:そうですね。仕分けのスピードに対してピッキングが追いつかないという状況が課題になっています。現在は12オーダー分、だいたい80ピースをピッキングして仕分けるという工程にしています。
もっと一度にピッキングできる量を増やせると更に効率よく進められると思いますが、商品数も約300種類あるのですぐには難しい状況です。
ピッキングにかかる時間は人によって差はあるのですが、早ければ5分、少し時間がかかると10分ぐらいです。新商品や人気商品は作業場から近い場所に配置してピッキングしやすくするなど、様々な改善をしてスピードを上げていきたいですね。
---- 基本はトータルピックで行っているのですか?
杉田様:ほとんどトータルピックです。例外として1オーダーの商品数が非常に多い場合などは、個別対応することもあります。新商品が多く発売されるタイミングではそのような対応をすることがありますね。
従業員教育の進め方
---- 教育はどのように進められているのですか?
杉田様:従業員を集めてデモンストレーションを行って教えたり、一人ひとり個別に教えたり様々です。
今まで教えた従業員は派遣の方や、梱包をやったことがない方が多いです。そこでまずはOmniSorterで実際に商品を流してもらいます。商品を流しながら一緒に商品理解についても教育するようにしています。
すると、「この商品は流すとバーコードが読み込めないね、こういう工夫をしないといけないね」など、色々なパターンが出てくるので、試行錯誤しながら一緒に作業を行っていきます。
その後は、カートの取り外し方やコンテナの設置の仕方、バーコードの読み方、電源の入れ方切り方など、順々に教えています。一気に全てを教えようとするとパンクしてしまいますので、1個ずつ覚えたかどうかを確認してから次の工程に進んでいくようにしています。
---- 教育をしてOmniSorterに慣れるまで何日ぐらいかかるものでしょうか?
杉田様:大体1週間ぐらいです。そこで任せられるかどうかを判断して、できる人には更に教えて伸ばしていったり、フォローが必要な人にはアドバイスしたりなど、人によって対応を変えています。
今後のロボットに期待すること
---- OmniSorterを導入したことについて、山口様の感想をお聞かせください。
山口様:まだ運用開始してから数か月なので機械への慣れや、教育面で属人的に運用している部分があります。ですが、それらがクリアされスムーズになると、OmniSorterは現場で絶対に必要な存在になってくると思います。
現場が最大限に機械の性能を発揮するために改善すべき点がまだまだあります。人の導線や動き方だったり、手前の工程と後工程だったり、どうやって効率を上げられるかを現状から変えていく必要があります。
このような部分も人間とロボットの共存です。人間の成長に伴って着実に効果も現れると感じています。
---- 今後のロボットに期待していることはありますか?
山口様:これは多くの物流会社がそうだと思うのですが、最終工程の商品を梱包するところですね。
通販となると商品の種類がたくさんあります。ガラスや陶器、ぬいぐるみ、Tシャツ、シールなど。それこそ、吸引をかけるとパッケージのフィルムが壊れてしまうような商品もあります。
このような人間の指先にある触感のような要素を、AIのビッグデータの中で、商品情報とカメラ画像からの解析によって、どのように吸引すれば物が壊れずにスムーズに入れられるのか。難しいとは思いますが、それができると物凄く楽になりますね
ロボットも進化しているとはいえ、指先の繊細な作業はまだまだですよね。そのような部分の進化に期待しています。
---- お話いただいた理想を実現できるよう、弊社も今後のサービス向上に努め、引き続き自動化の様々なご提案をさせていただければと存じます。本日はありがとうございました!
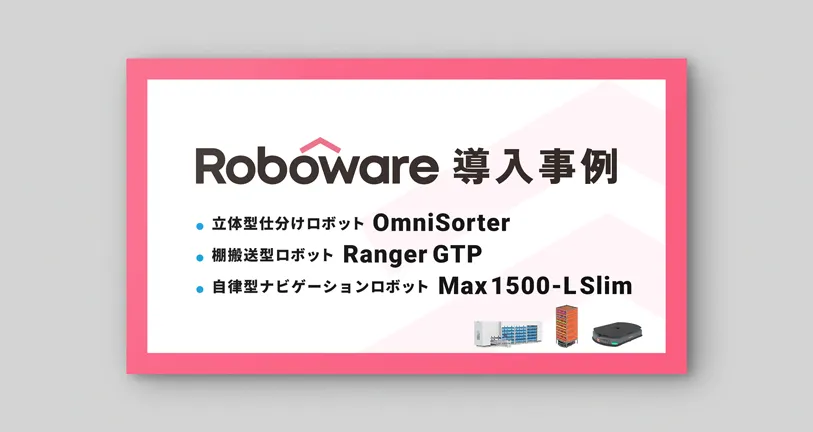
Latest Case Study 最新導入事例